有一则故事是这样说的:
我国古代的魏文王问名医扁鹊说∶“你们家兄弟三人,都精于医术,到底哪一位医术最好呢?”扁鹊答说∶“长兄最好,中兄次之,我最差。”文王吃惊地问∶“你的名气最大,为何说长兄医术最高呢?”扁鹊惭愧地说∶“我扁鹊治病,是治病于病情严重之时。一般人都看到我在经脉上穿针管、在皮肤上敷药等大手术,以为我的医术高明,因此响遍全国。我中兄治病,是治病于病情初起之时。一般人以为他只能治轻微的小病,所以名气只及于本乡里。而我长兄治病,是治病于病情发作之前。一般人不知道他事先能铲除病因,所以觉得水平一般,但我看来他水平最高。”
这则故事中的三位医生看病水平,就如同我们的质量管控水平。目前,我们的质量工作还仅仅停留在质量检验阶段,即头痛医头脚痛医脚,问题出在哪里,就集中管控哪里。然而,这种管控已经成为事后管控,不合格品已经产生,已然造成质量成本的浪费。
日本著名的质量专家石川馨指出:“质量是制造出来的,而不是检验出来的。”在质量工作中重点是预防质量问题的发生,而不是完全依靠事后的检查。那么如何才能有效地“预防缺陷”呢?FMEA(潜在失效模式和效果分析)就是一种常用的方法,也是目前公认的行之有效的方法。
风险分析的基本目的在于回答如下两个问题:一是,什么容易出错?二是,如果错误发生了,其发生的概率有多大?其结果如何?与旧的质量管理方法比较来看,FMEA注重预防问题而不是解决问题,消除浪费而不是处理浪费,降低不可靠性而不是量化可靠性。
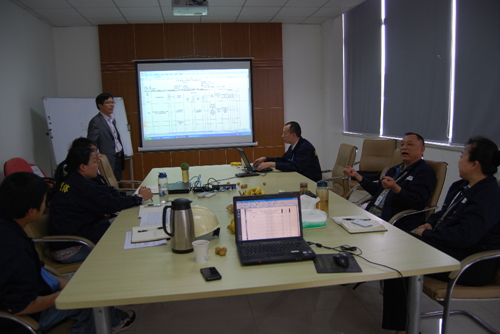
在为期 近2个月的FMEA培训中,由管理副总李智慧和运营副总李荷庆带领,在老师的辅导下,质量、研发、生产等三个部门联合,就超纯氨项目中所有工艺进行头脑风暴,就每一个操作工序进行失效模式分析。
例如:就氨气加料中的一道工序进行如下分析:
步骤1.加料要求为:对非工作组汽化器添加原料至140cm以下
步骤2.失效模式描述为:液位过高
步骤3.造成的影响为:液氨大量气化导致压力过高,安全阀起跳
步骤4.评定该项的严重度,进行打分
步骤5.造成失效模式的原因分析为:进料泵关闭时间延迟
步骤6.如何进行预防措施管控:设定液位,每釜每次记录
步骤7.评价发生度及探测度的比分,就三项比分的乘积判定该道工序是否受控,是否需要改进措施?
步骤8.建议措施:增设液位报警器,实现液位报警与阀门关闭的联动装置
步骤9.明确责任部门及完成期限
步骤10.再次衡量改进后方法的严重度、发生度和探测度。
就这个事例可以看出,FMEA分析并不是深奥的管理理论,而是行之有据的预见性缺陷分析的一种思维,它可以广泛的应用于企业管理的各个层面。作为产品生产的主要实现者,各生产车间的管理者,如果能够将这种思维模式渗透到生产管理的每个细节中去,将会是多大的一笔财富啊!
金宏推行质量管理并构建符合国际标准的质量管理体系是一项系统工程,它需要各个部门的全力合作。面对现代市场的不断变化,只要我们始终坚持先进的理念为指导、企业全员参与、以质量为核心的质量管理工作思路,强化管理、勤奋工作、准确定位、合理实施,就一定能提高企业的核心竞争力,扩大市场!